Accelerating Medical Device Manufacturing with Forward-Thinking Innovation
Large and small manufacturers alike continue to see a growing shift toward smaller, smarter medical devices as they strive to scale up production and double down on the commercial potential for their current, next-generation and future devices. In their quest to speed up product design and development, many companies outsource to contract development manufacturing organizations (CDMOs). However, most CDMOs lack the core technical capabilities required for manufacturing micromedical components, sub- assemblies, and final assemblies, hindering companies from innovating faster to accelerate their path to market. This is where Intricon Corporation can make a big impact.
Intricon is a leading contract development manufacturer in micromedical technology and collaborates with medical device OEMs on device design, development, and manufacturing. The company is focused on micromedical components, sub-assemblies, and the production of final medical devices. Its wide range of capabilities in precision miniature molding, microelectronics, device assembly, and wireless communication and its proactive support are vital in driving program performance while delivering excellent outcomes.
“We are exclusively focused on medical devices, which are helpful to companies bringing wearable biosensor devices into clinical use. Our longstanding legacy in developing medical wearables means we understand the vocabulary and approach needed to take a device from concept all the way to the market,” states Dave Liebl, chief commercial and technology officer at Intricon.
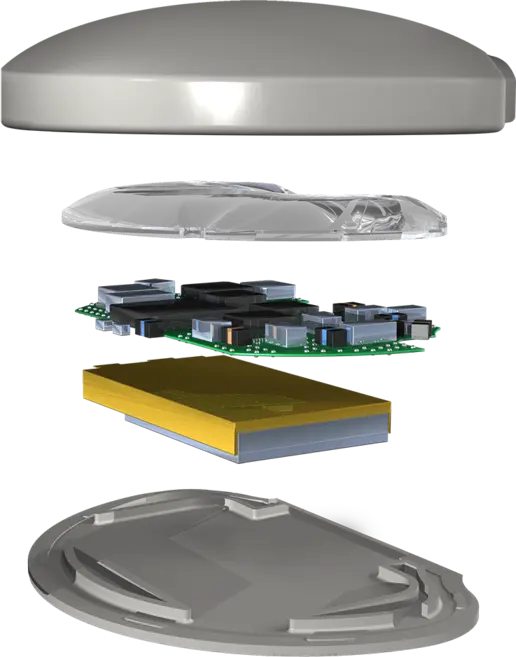
Intricon’s roots are in medical wearable devices, dating back more than 45 years to when the company developed its first hearing aid, a precursor to modern patient monitoring devices. As the company’s hearing health business grew, Intricon managed its own regulatory filings and design history files, both in the U.S. and Europe. Dave Liebl explains, “We are unique in that we also do our own devices. In the hearing health space, we create and manage our own design history files, design dossiers, and our own regulatory submissions. The fact that we do this gives us the ability to help our customers be more proactive because we already know the key questions to drive their project forward effectively.”
Over time, as demand for patient monitoring devices grew, Intricon knew there was an increasing need to build smaller, lighter, cheaper, and more comfortable products. But building such a next-generation device can be challenging in every way, from internal passive components to external form factors. With an understanding of miniaturization processes and precise technical requirements, Intricon has helped numerous medical device manufacturers reduce device footprints while avoiding secondary complications for their devices.
Intricon has robust, vertically integrated capabilities for making patient monitoring devices real while eliminating the need for companies to work across multiple suppliers. The Intricon team combines its expertise in high-density microelectronics with the ability to create miniature custom- molded carriers and chassis for patient monitoring devices.
The company has strong firmware development and wireless communication expertise, including Bluetooth and Bluetooth Low Energy (BLE). With a technology set vertically integrated under one roof, combined with its history of in- house medical device development, Intricon is able to help companies shorten the time to market for their devices.
It can assist with the design for manufacturability (DFM), helping companies make their devices not only better but less expensive. According to Liebl, companies frequently come to Intricon with pre-conceived ideas about a device’s potential configuration and layout. They then benefit from Intricon’s experienced teams that bring ideas the client hasn’t yet considered. Liebl explains, “We’re able to look at the device with fresh, experienced eyes, and may see it a little differently. We then suggest ways to save money, make the device more reliable, and effectively scale production. This advice addresses key pain points for medical device manufacturers.”
Our longstanding legacy in developing medical wearables means we understand the vocabulary and approach needed to take a device from concept all the way to the market.
Intricon uses a proven development process, collaborating with clients through the entire journey to bring their devices to life, from DFM, development (particularly for second- and third-generation devices), manufacturing, regulatory approval, and commercialization. Throughout the process, Intricon teams seamlessly communicate with clients to make sure all quality and regulatory requirements are met. Intricon also formulates up-front suitable testing and inspection strategies and provides ideas to streamline the supply chain.
This collaboration and industry expertise are key to Intricon’s success. The company constantly emphasizes side-by-side collaboration with clients in their product development endeavors, ensuring everyone receives the best and brightest team to achieve the ultimate goals for the final product.