Tolerance stack-up is a defining design concept to ensure new products are built efficiently and effectively.
At a time when the future of micro miniature medical devices seems unlimited, one fundamental reality remains firmly in place — the sizes and shapes of human anatomy.
From blood vessels to ear canals, respiratory passages to neural pathways, the physical dimensions of the body available for life-saving and life- enhancing medical therapies exist within a minimum and maximum range. For medical devices, the general rule for reaching deeper into the tiniest areas of the body is “the smaller, the better.”
In theory, a single medical device can do many things even in the smallest anatomical feature. In actuality, building a multi-functional micromedical tool and incorporating the electronic circuits that may be required to empower it calls for proven expertise from the earliest stages of design all the way through to full-scale production. The greater the density of componentry, the more precision and validation is required for reliable performance.
Tolerance stack-up is a defining concept for designing new products to ensure they’re built efficiently and effectively during production, and it’s much more than a theoretical construct. It’s how the device is constructed with all layers of functionality — electrical, mechanical and software/firmware — working together according to specification and within performance requirements, the sum total determining the eventual success for producing the device.
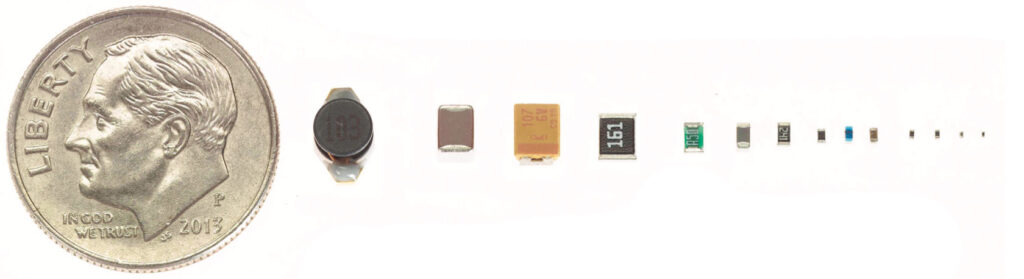
Electrical: Where one one-thousandth counts — a lot
Even a microelectronic circuit so small a half dozen could fit onto the surface of a dime can include multiple active and passive components, metallic wiring, traces and vias on the circuit board, memory units for device instructions and more.
How the layers relate to each other influences more than the overall reliability of the device. The relationship also determines the manufacturing viability and production costs of the product. In this case, the components, materials, and manufacturing tolerances can refer to both the physical dimensions of the parts and performance parameters.
In terms of product efficacy, most people will never know the critical difference made by a half of one-thousandth of an inch in the positioning of electrical components and sub-assemblies. However, in terms of production, optimal positioning can mean higher yields which keep costs lower and lead to more finished devices in market to meet the needs of clinicians.
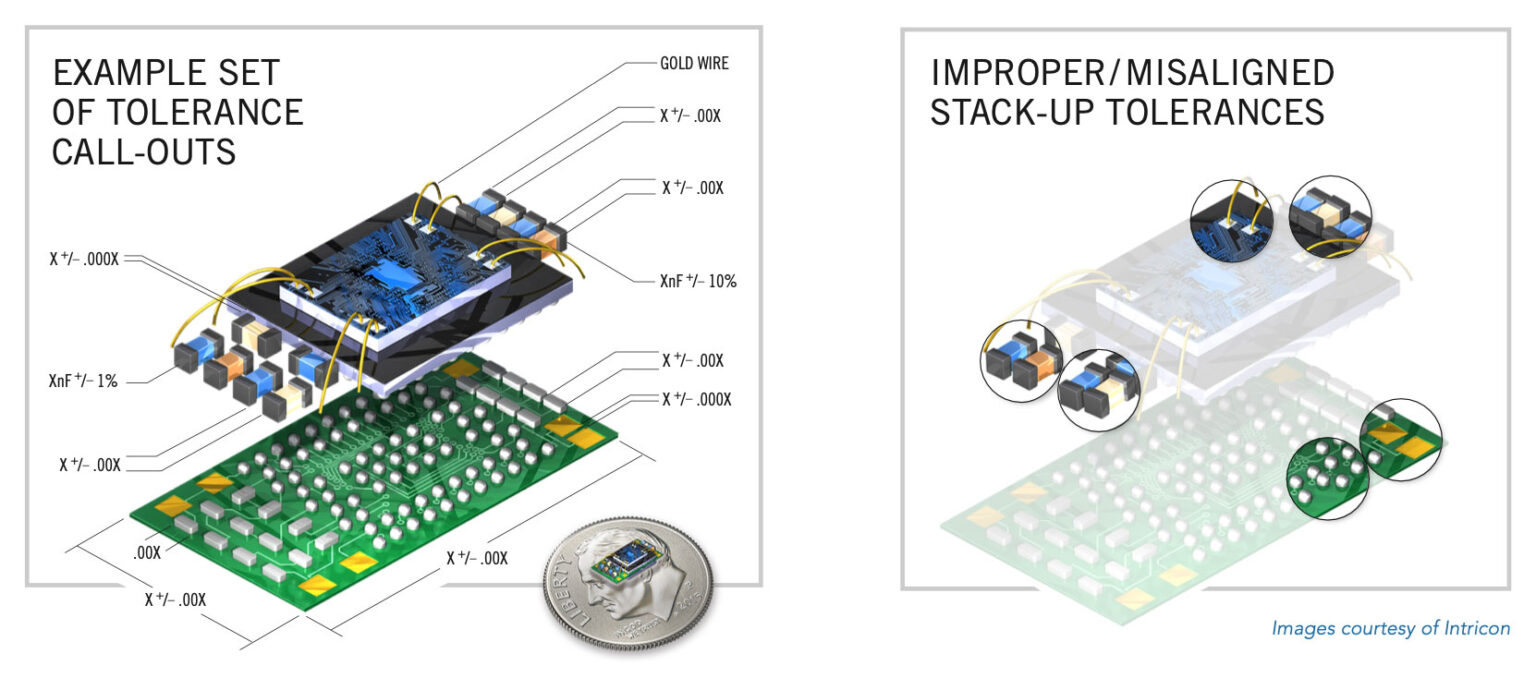
Mechanical: Physical tolerances play a part, too
Body-worn devices typically incorporate input sensors, device controls, output functionality, power supplies or charging ports and more. Interventional surgical tools often add navigational aids such as electromagnetic sensors. These devices can also include low-power communications capabilities.
Specifying, sourcing and incorporating the mechanical parts of a medical device adds even more layers to the tolerance stack-up along with the electrical tolerances and “cross-talk” of the active and passive components.
Some components already exist. Some components can be modified. And some components require all-new design, testing and production. Before the production lines start rolling at full capacity, all tolerances must be evaluated and validated.
Software/firmware: Onboard intel at work
At the heart of today’s high density, micro miniature medical devices are the instructions that flow through the electrical circuitry and drive the mechanical assemblies.
As devices get smaller and smaller, more functionalities require more memory. Accommodating this requirement adds an extra layer of complexity to the intricate tolerance stack-ups within the device.
Supply chain considerations: Different suppliers may have different specifications
Now more than ever, supply chain management figures prominently into sourcing and manufacturing assemblies and sub-assemblies needed for micro miniature medical devices.
Specialized components are often available from more than one supplier, but knowing which source can actually meet the tolerance specifications required for cost-effective, high-volume manufacturing can only come from experience, not trial and error.
More device capabilities mean tolerance stack-up is even more important
Looking ahead, micro miniature medical devices will continue to do more and more, particularly with data that’s generated, stored and transmitted during a procedure or on an ongoing basis for body-worn devices.
Integration with cloud-based applications that harness the power of machine learning and insights of artificial intelligence places expand the potential of every medical device even as the physical dimensions of human anatomy remain constant.
Taking into account the ever- increasing complexity of tolerance stack- ups and designing for manufacturability is critical to ensure continued innovation in medical device engineering.