The Project
An innovative medical company sought a manufacturing partner for a novel EM tracking device to be used in orthopedic and neuro surgery. The company initially turned to Intricon solely for its electromagnetic (EM) sensor expertise—then discovered how its Design for Manufacturing and vertical integration capabilities could yield a higher-quality, fully-functional device at lower cost.
The Challenge
The initial project consisted of incorporating EM sensors into the device. The client requested off-the shelf vs. custom microcoils as they assumed customization would be expensive and time-consuming. But the Intricon team immediately identified inefficiencies in the original design. The original designs not only overcomplicated sensor placement, but they also required unnecessary molding and assembly processes that would drive up costs, diminish quality, and impair performance. The project quickly evolved from straightforward sensor assembly into comprehensive one-stop manufacturing.
The Solution
Rather than an off-the-shelf sensor, Intricon’s in-house engineers designed a custom, highly-manufacturable sensor in three weeks that cost 50% less. The team also developed efficient molding and assembly processes that guaranteed accurate, consistent sensor placement, reliable performance, and significantly reduced costs. Although the project scope initially covered the EM sensor only, the Intricon team provided not just a superior sensor, but also a valued-added assembly, molding, and attachment—ultimately, a fully functional device ready to be sent to the client’s customer. By leveraging Intricon’s DFM and vertical integration expertise, the client was thrilled with the efficiency of receiving a comprehensive custom solution of superior quality and minimized cost from a single CDMO partner.
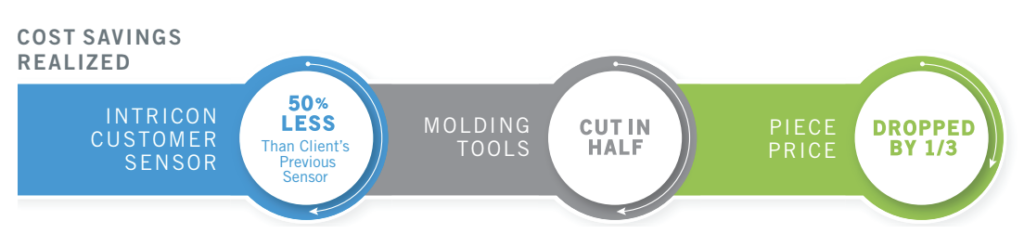