Case Study: Facing a Distressed Supply Chain, a Major Medtech Company Leverages Intricon to Accelerate the Redesign Process by 140%
THE PROJECT
A major medtech innovator’s supply chain became distressed when its existing supplier couldn’t resolve a product failure. The failure left existing patients without usable devices and threatened the company’s ability to meet future production demands. Seeking a rapid solution from a preferred vendor, the company turned to Intricon to find a solution.
THE CHALLENGE
The Intricon team identified design and manufacturing flaws that led to the device’s performance issues. They determined that a solution required more than design tweaks; rather, a total redesign of the molded subassembly was needed. Facing pressure to rapidly address the field failures, the Intricon team managed through complex supply chain shortages and long lead times. In addition, they coordinated a broad cross- functional group of stakeholders at the client – including quality, design engineering, production, and supplier management – to efficiently drive the product redesign process to completion.
THE SOLUTION
Intricon redesigned the product with an optimized form factor, an improved heat stake profile, and increased tolerances that could withstand incidental pull forces and maintain a secure connection. While product redesigns typically take 18 to 24 months in the medtech industry, the Intricon team drew on its Design for Manufacturing (DFM) expertise to navigate from problem identification to product validation in just 10 months, 2.4 times faster than traditional development, accelerating the redesign process by 140% (Fig. 1). The client was able to restore its ability to meet pent-up demand for over one million parts.
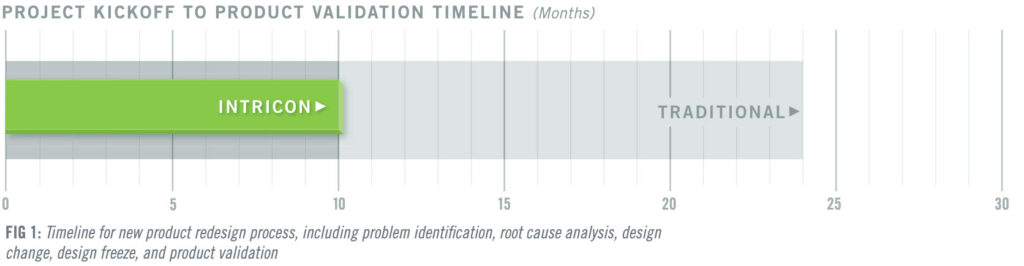