Insights Engineered for MedTech Innovators
Explore case studies, technical insights, and thought leadership from the experts behind the industry’s smallest, smartest devices.
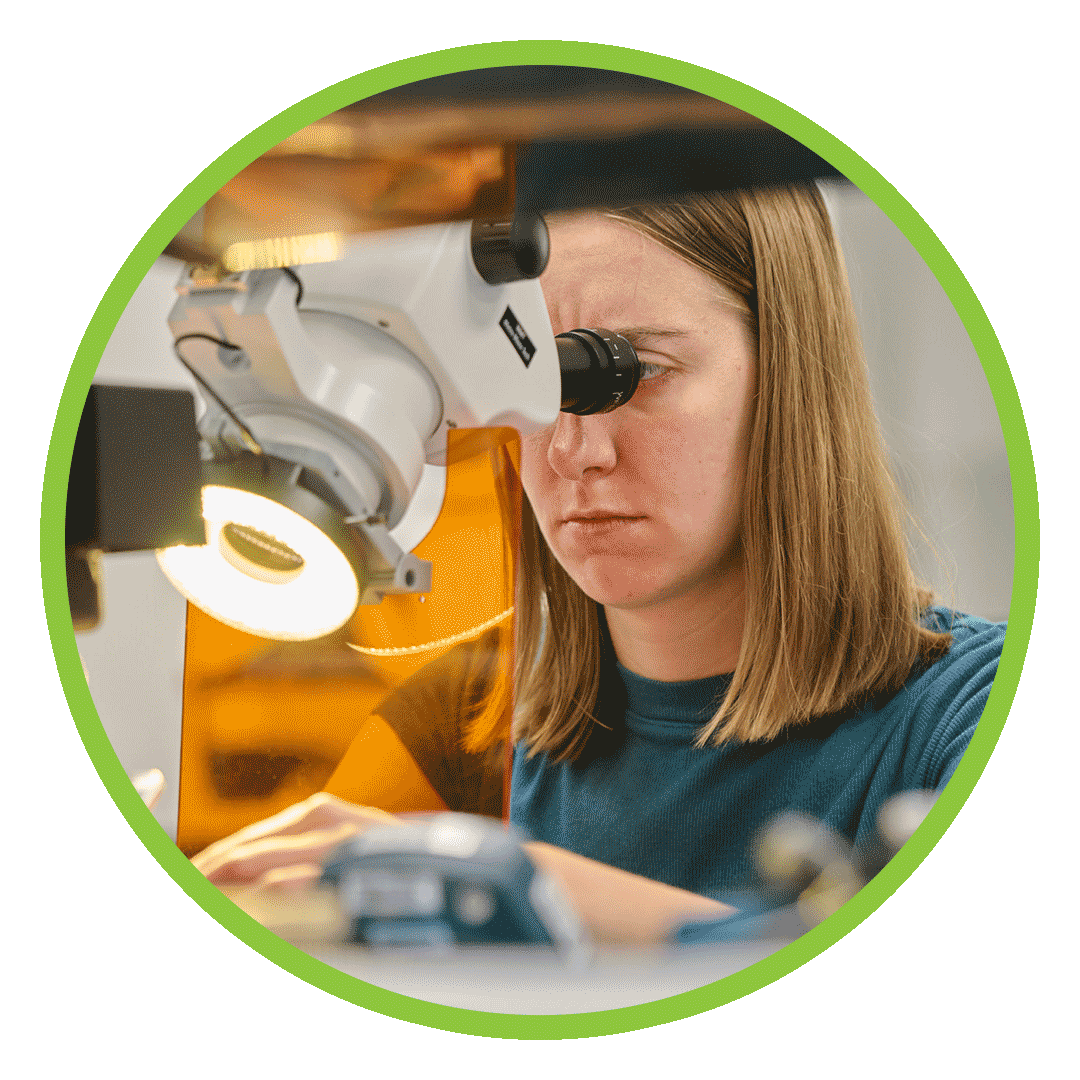
ALL
Case Studies
Thought Leadership
Podcasts
Explore case studies, technical insights, and thought leadership from the experts behind the industry’s smallest, smartest devices.
ALL
Case Studies
Thought Leadership
Podcasts